Value Engineering (VE) in construction is the process of enhancing design performance, managing cost, and delivering long-term value. It is a structured, collaborative method that reviews how a project delivers its intended function and identifies smarter, more efficient ways of achieving it.
From Firminger’s perspective, Value Engineering is about improving a project’s function-to-cost ratio without compromising on quality, compliance, or operational performance. Our team-based approach focuses on cost optimisation, design efficiency, and the sustainable use of resources throughout the construction lifecycle.
Our RICS qualified cost consultants are uniquely positioned to support clients with both Value Engineering and Value Management.
Understanding Value Management
vs. Value Engineering
Value Management (VM) is the broader, strategic process that takes place in early design stages. It involves the Quantity Surveyor advising the design team on construction methods, material choices, and project risks. VM supports the alignment of the project brief with the client’s business objectives.
Sustainability is now central to this process. Our advice addresses not just upfront construction costs, but also operational performance, energy use, and the life cycle benefits of alternative options.
Value Engineering, by contrast, is a more targeted activity. It typically occurs during RIBA Stages 3–4, and focuses on refining the design for cost, buildability, and programme
Value Engineering Driving Cost Optimisation Without Compromising Quality
At Firmingers, we deliver structured Construction Value Engineering services that help clients get the most from their investment without reducing quality, performance, or compliance. VE is not about cutting corners; it’s about working smarter by challenging assumptions, analysing design intent, and assessing more efficient alternatives.
We apply value engineering techniques throughout the pre-construction and design stages, ensuring that every decision contributes to the project’s success in terms of cost, buildability, and ongoing performance.
What is Value Engineering and How Does It Work?
Value Engineering is a formal process that reviews key design components and construction methods to identify opportunities for:
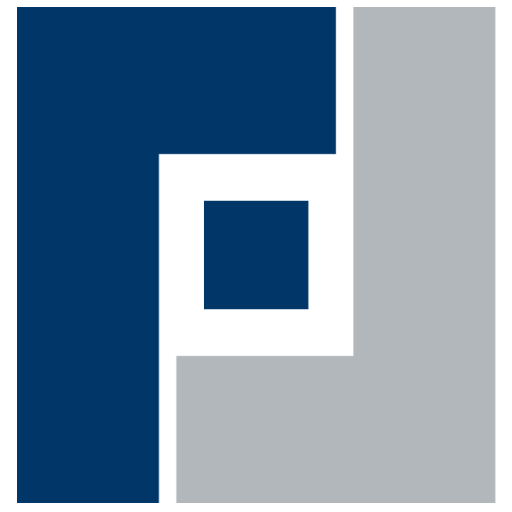
Cost savings
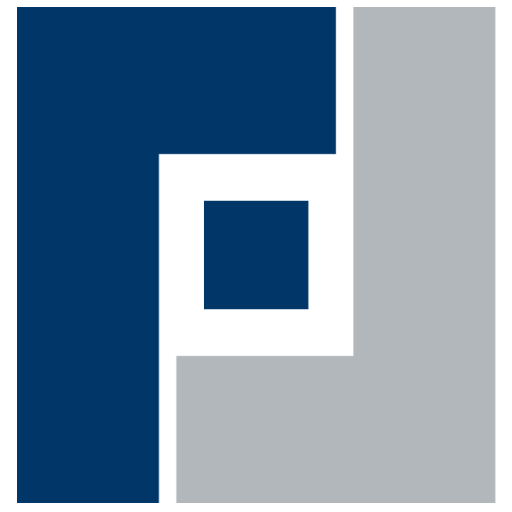
Improved efficiency
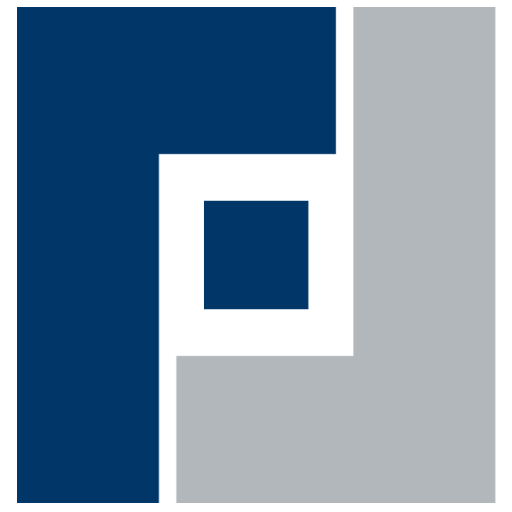
Faster delivery
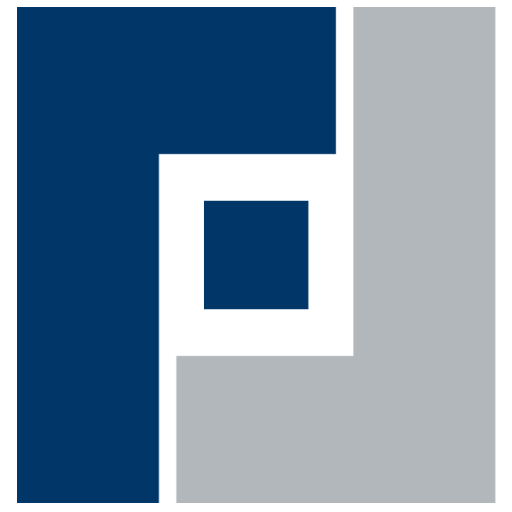
Enhanced life cycle performance
The process begins by analysing how different elements of the design deliver their intended function. From there, we identify alternative approaches that may reduce cost, risk, or time; all without sacrificing quality.
Value Engineering Involves
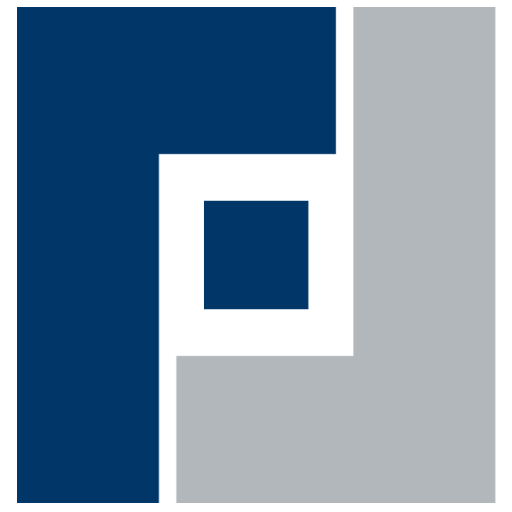
Identifying the main elements of a product, service or project
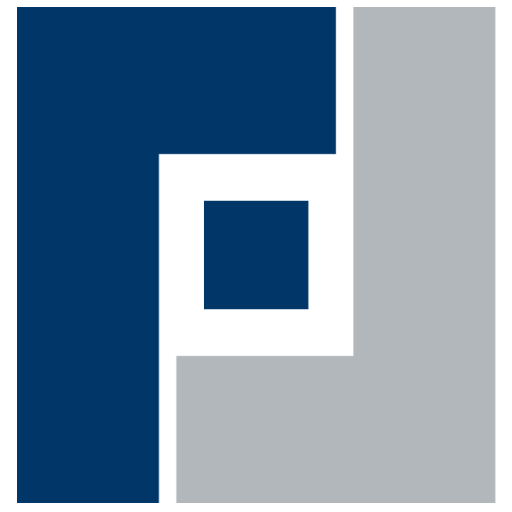
Analysing the function of those elements
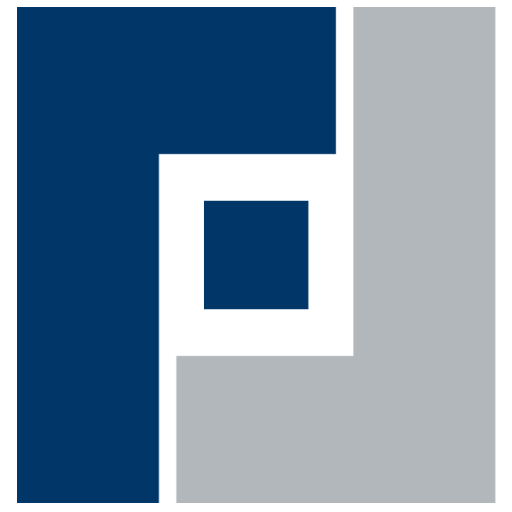
Developing alternative solutions for delivering those functions
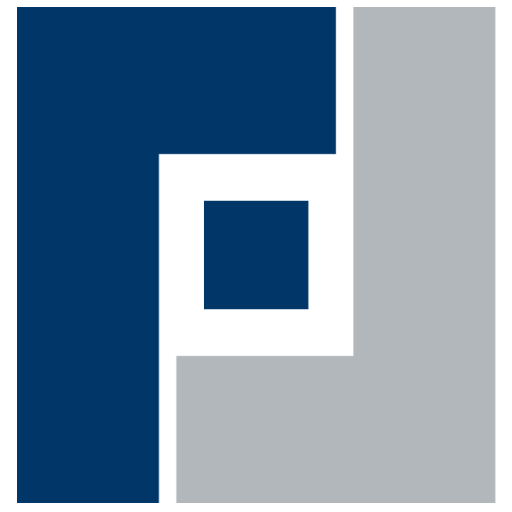
Accessing the alternative solutions
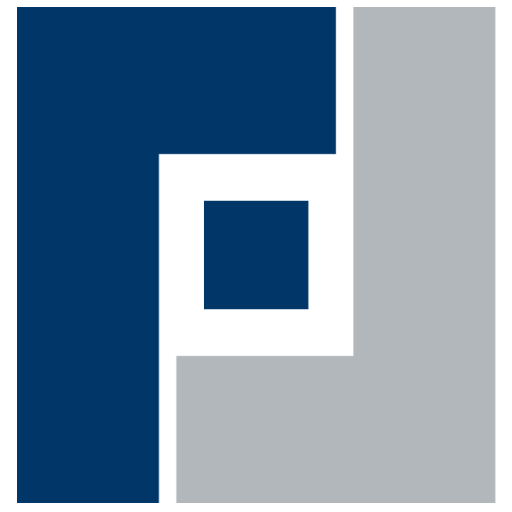
Allocating cost to the alternative solutions
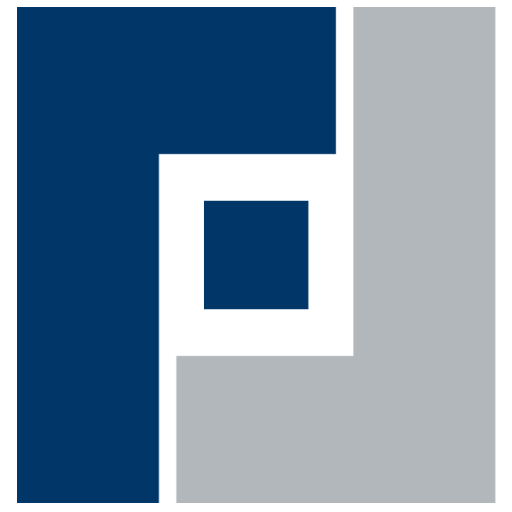
Developing in more detail the alternatives with the highest likelihood of success
The Firmingers Method –
Value Engineering in Practice
We typically follow this five-step process:
1. Understand the problem – Identify cost or performance challenges
2. Explore alternatives – Develop viable solutions
3. Evaluate and compare – Assess cost, impact, risk and practicality
4. Develop the best option – Refine the preferred solution
5. Implement and monitor – Embed changes and track benefits
This approach is fully collaborative, requiring input and buy-in from the client, design team, and – in two-stage tender processes – the contractor. Contractors often provide valuable insight into buildability and procurement options.
The Key Characteristics of Value Engineering:
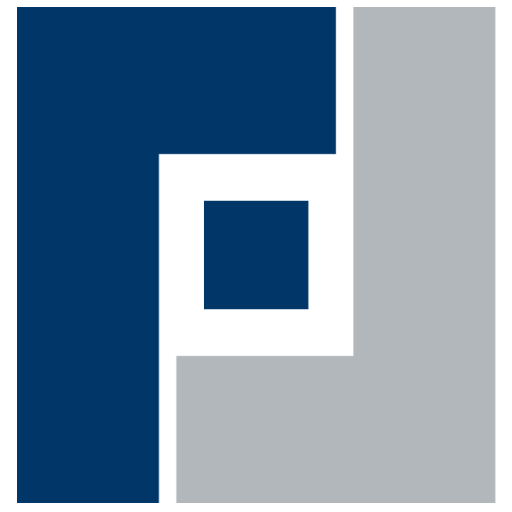
Applied during design development (usually RIBA Stages 3–4)
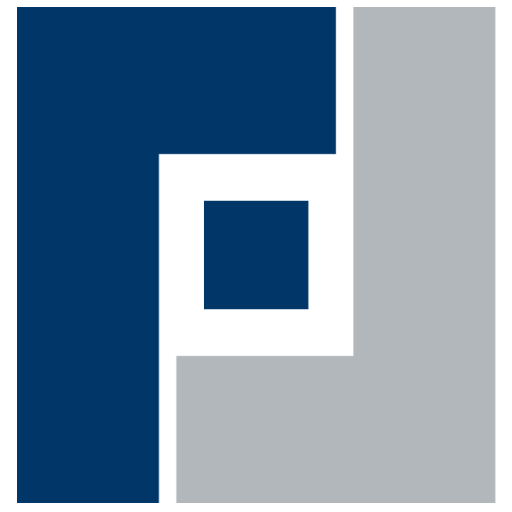
Focuses on cost, buildability, and functionality
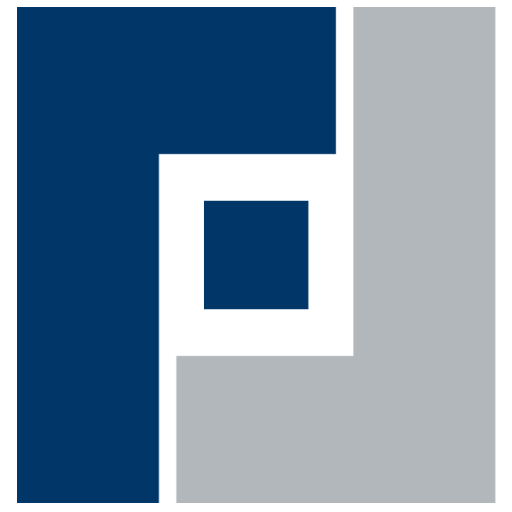
Reviews specific materials, components, and construction methods
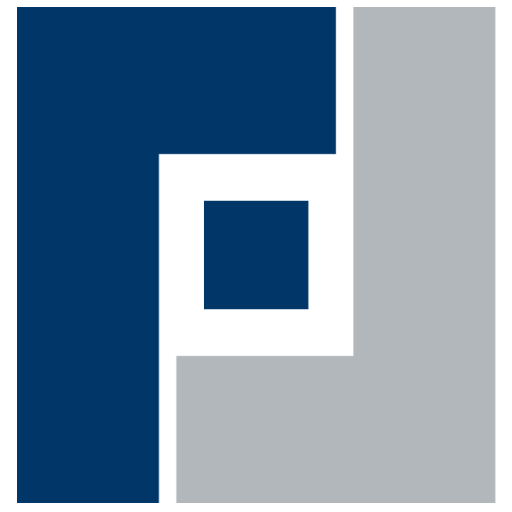
Involves option generation and assessment
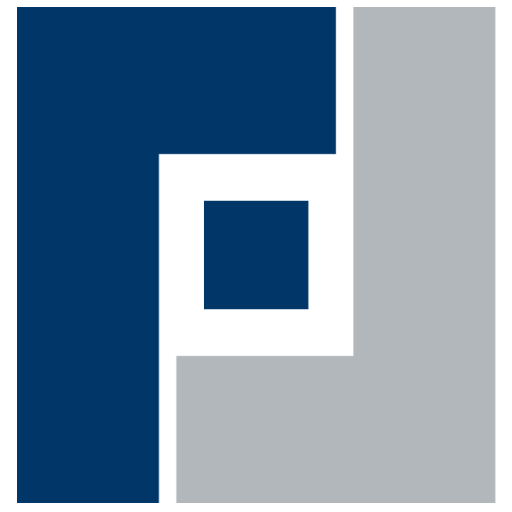
Can result in capital cost savings, life cycle improvements, or programme gains
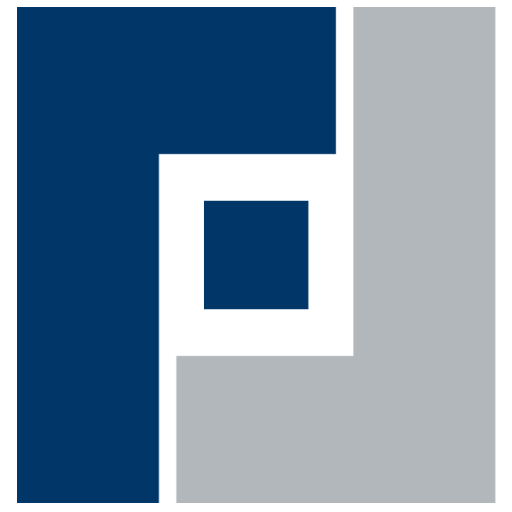
Requires buy-in from the full design team, client, and often the contractor
When Should Value Engineering Be Introduced?
The earlier, the better. Changes made late in the design or construction phases tend to be more costly and disruptive. At Firmingers, we encourage VE discussions during early design development to ensure smoother integration and greater return on effort.
We support clients with structured VE workshops, clear documentation, and cost-benefit analysis that enables informed, auditable decisions.
Result accelerators:
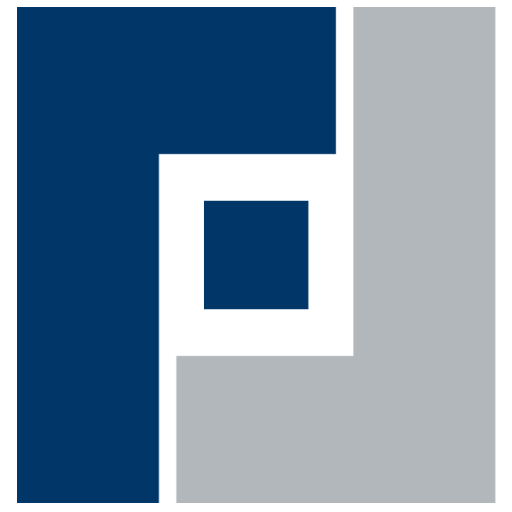
Avoid Generalities
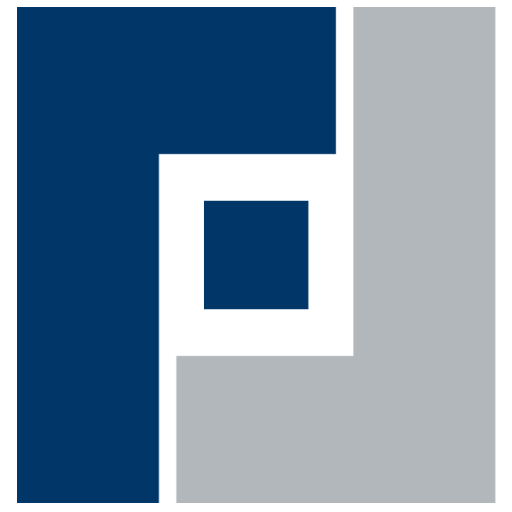
Get All Available Costs
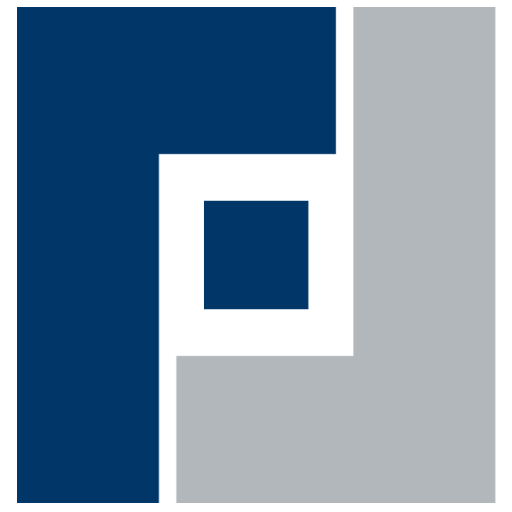
Use Information From The Best Source
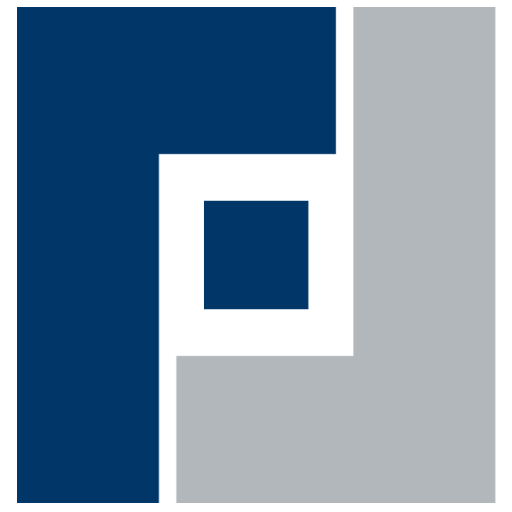
Be Creative
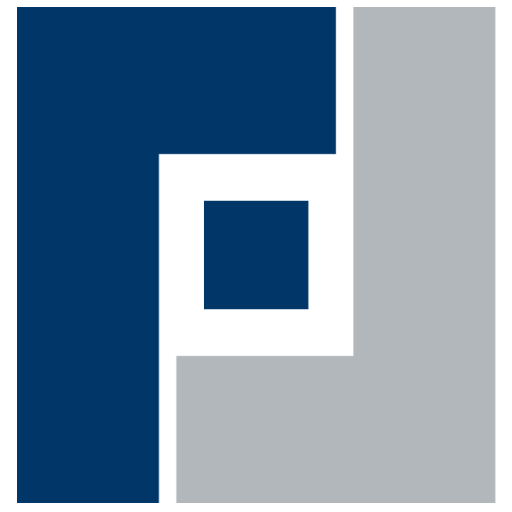
Identify and Overcome Road Blocks
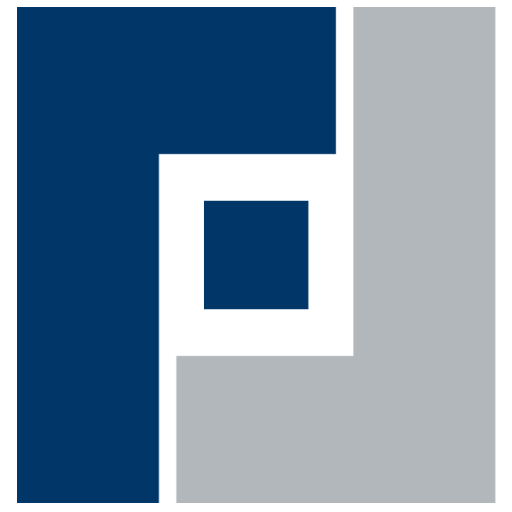
Use Industry Experts
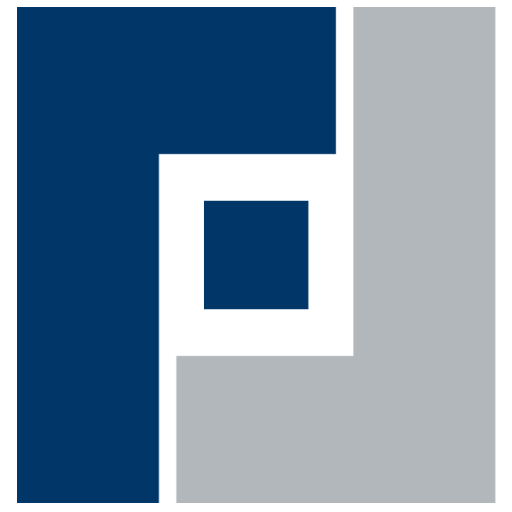
Price Key Tolerances
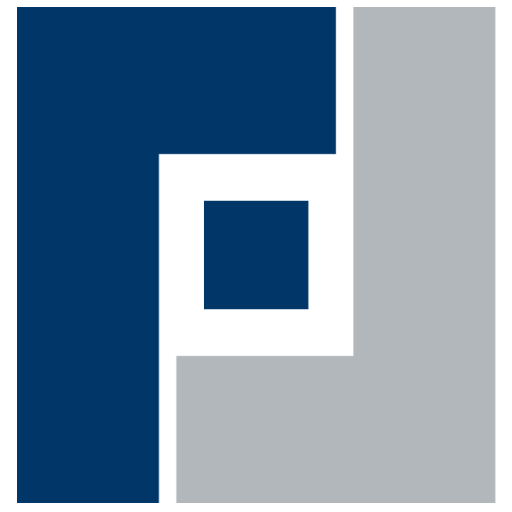
Use Standard Products
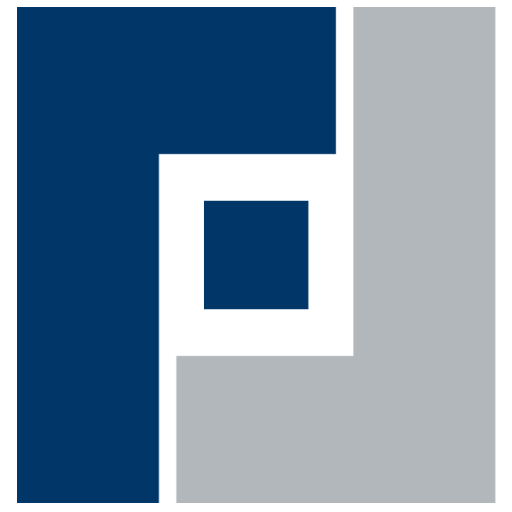
Use Expert Advice
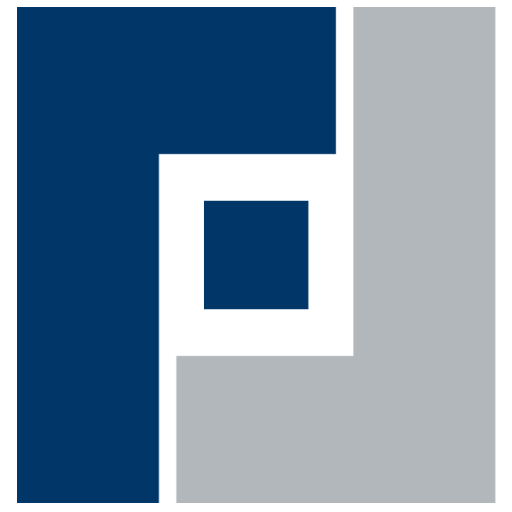
Use Specialists Processes
What Does Value Engineering Assess?
It involves identifying the main elements of a project. The Cost Manager will analyse the labour and material elements and look at installation costs and sequencing, M&E systems and energy use costs and life expectancy. Alternate solutions will be assessed to determine what does and does not add value by allocating costs to each alternative. Changes are ranked by impact and ease of introduction. The team can then determine which can be introduced to help the client find the best value solution.
Firmingers’ Approach to Construction Value Management
At Firmingers, Value Engineering is not an exercise in cost-cutting; it’s a tool for design refinement and risk control. We combine benchmarking, technical knowledge, and commercial understanding to:
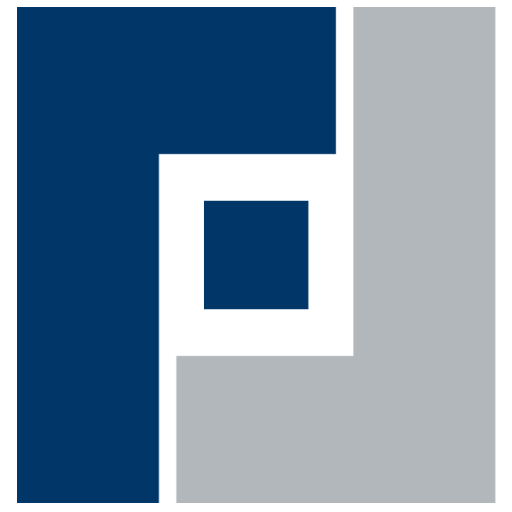
Optimise cost without compromising quality
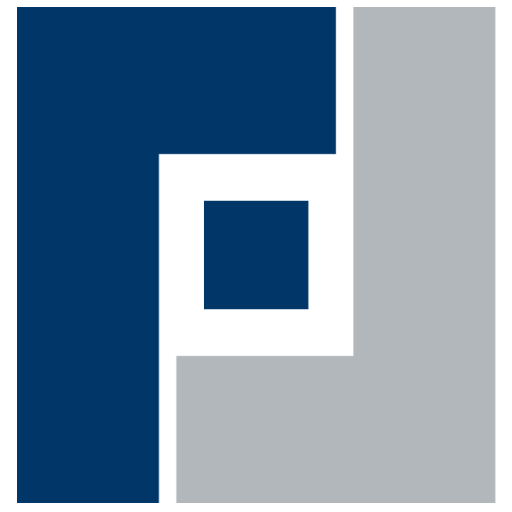
Align construction methods with programme goals
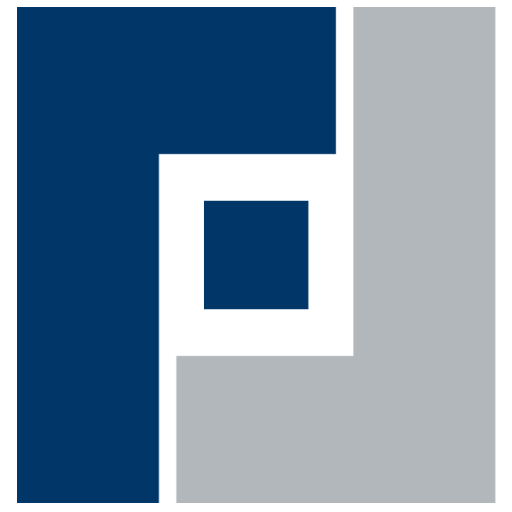
Improve sustainability and operational outcomes
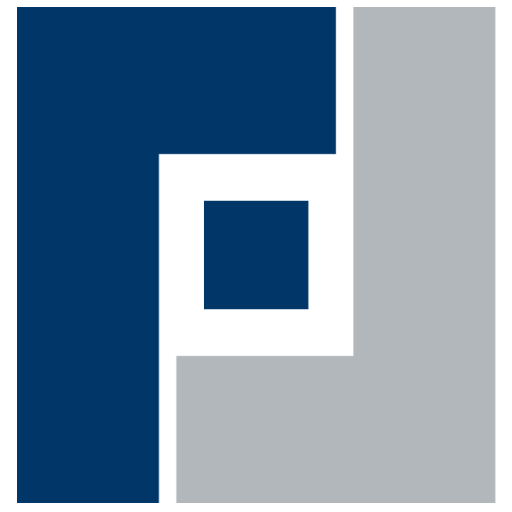
Bring tenders back in line with budget, if required
We act as facilitators and advisors throughout the process, ensuring decisions are technically sound and commercially aligned.
At Firmingers, Value Engineering is a collaborative, data-led process that helps deliver the right solution at the right cost. We work closely with the client, design team and contractor to evaluate alternative options that enhance value, reduce waste, and optimise long-term building performance.